A Guide To Wall Shear Stress Measurement - #2 - Indirect Measurements
Blog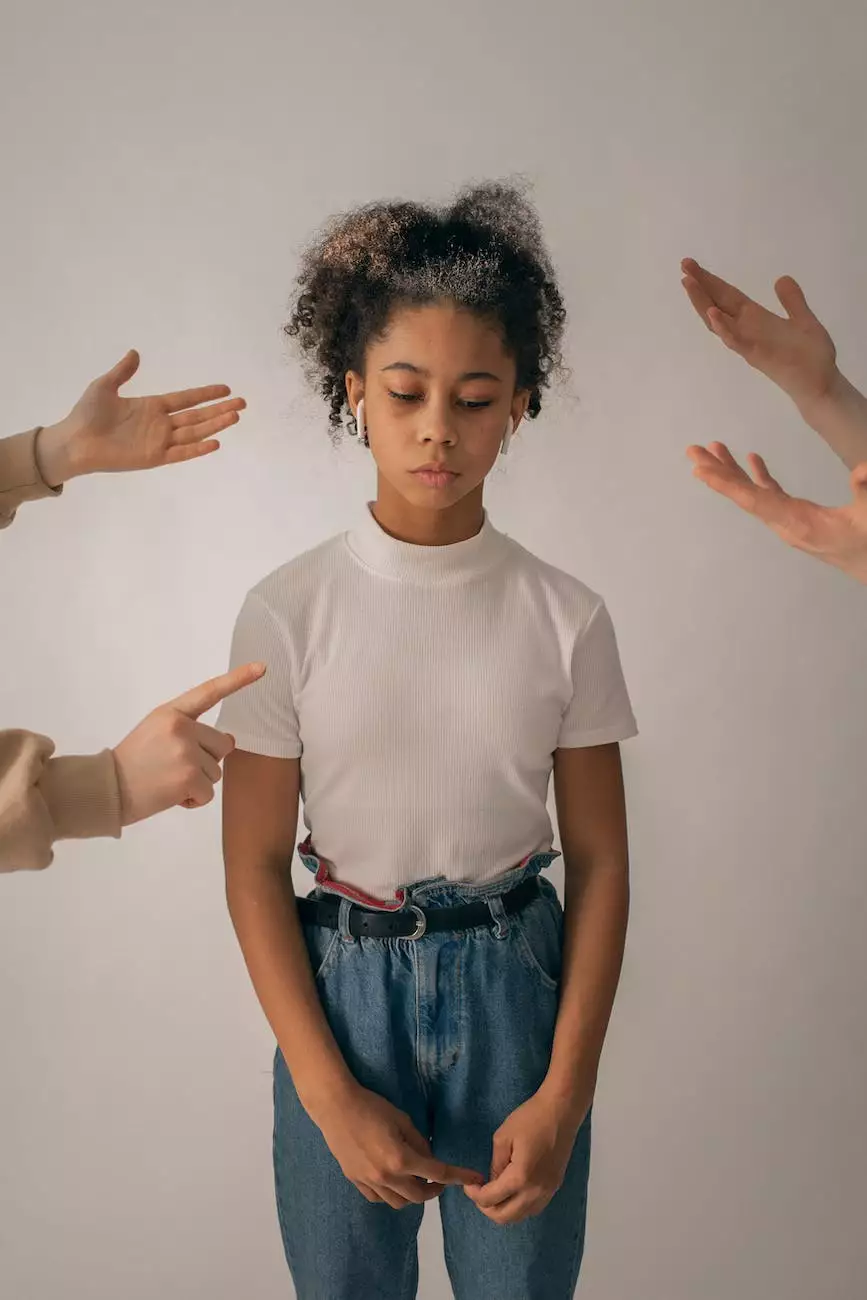
Welcome to Plastic Molding Pros, your trusted source for expert guidance on plastic molding processes in the eCommerce & Shopping - Manufacture category. In this comprehensive guide, we will explore the intricacies of measuring wall shear stress, specifically focusing on indirect measurement techniques. Understanding how to effectively measure wall shear stress is crucial for optimizing the quality and efficiency of plastic molding processes.
What is Wall Shear Stress?
Wall shear stress is a critical parameter in plastic molding that determines the force exerted on the surface of the mold during the flow of molten plastic. It plays a significant role in the formation of the final product's structure and surface quality. Measuring wall shear stress accurately allows manufacturers to adjust process parameters for optimum results.
Direct vs. Indirect Measurement Techniques
While direct measurement of wall shear stress provides highly accurate results, it typically involves complex and expensive instruments. Direct techniques require embedding sensors directly into the mold, which can be impractical for many applications. As a result, many plastic molding professionals rely on indirect measurement techniques, which provide a more accessible and cost-effective solution.
Laser Doppler Vibrometry
Laser Doppler vibrometry is a non-contact method used to indirectly measure wall shear stress. It involves analyzing the vibration characteristics of the mold surface induced by the flow of molten plastic. By correlating these vibrations with known wall shear stress values, accurate measurements can be obtained. Laser Doppler vibrometry offers the advantage of not affecting the mold's integrity or requiring extensive modifications.
Pressure Transducers
Pressure transducers are another indirect measurement technique commonly used in plastic molding. By strategically placing pressure sensors at specific locations within the mold, the differential pressure generated during the flow of plastic can be measured. This data can then be used to estimate the wall shear stress. Pressure transducers offer a more straightforward and cost-effective approach to indirectly measuring wall shear stress.
Mold Surface Temperature Gradient
Measuring the temperature gradient across the mold surface during the plastic flow provides valuable insights into the wall shear stress. As the plastic flows, variations in the mold surface temperature can be correlated to changes in wall shear stress. By carefully monitoring the temperature distribution, manufacturers can make informed adjustments to optimize the molding process.
Considerations for Indirect Measurement Techniques
While indirect measurement techniques offer practical solutions for measuring wall shear stress, there are some important considerations to keep in mind:
- Calibration: Accurate calibration of the measurement instruments is crucial to ensure reliable results.
- Mold Design: The mold design should be optimized to minimize potential interference with the measurement techniques, ensuring accurate readings.
- Process Conditions: Variations in process conditions, such as temperature and pressure, can affect the accuracy of indirect measurements. Consistency and control are vital for reliable data.
Conclusion
Measuring wall shear stress is an essential aspect of plastic molding, influencing the quality and efficiency of the process. While direct measurement techniques offer high accuracy, indirect methods provide a more accessible and cost-effective alternative. Laser Doppler vibrometry, pressure transducers, and mold surface temperature gradient analysis are just a few examples of indirect measurement techniques available. By leveraging these methods and considering the associated considerations, plastic molding professionals can optimize their processes for superior performance and product quality.
For more information and expert guidance on plastic molding, visit Plastic Molding Pros – your trusted partner in the eCommerce & Shopping - Manufacture sector!