3D Printing Evolves Sand Casting
Blog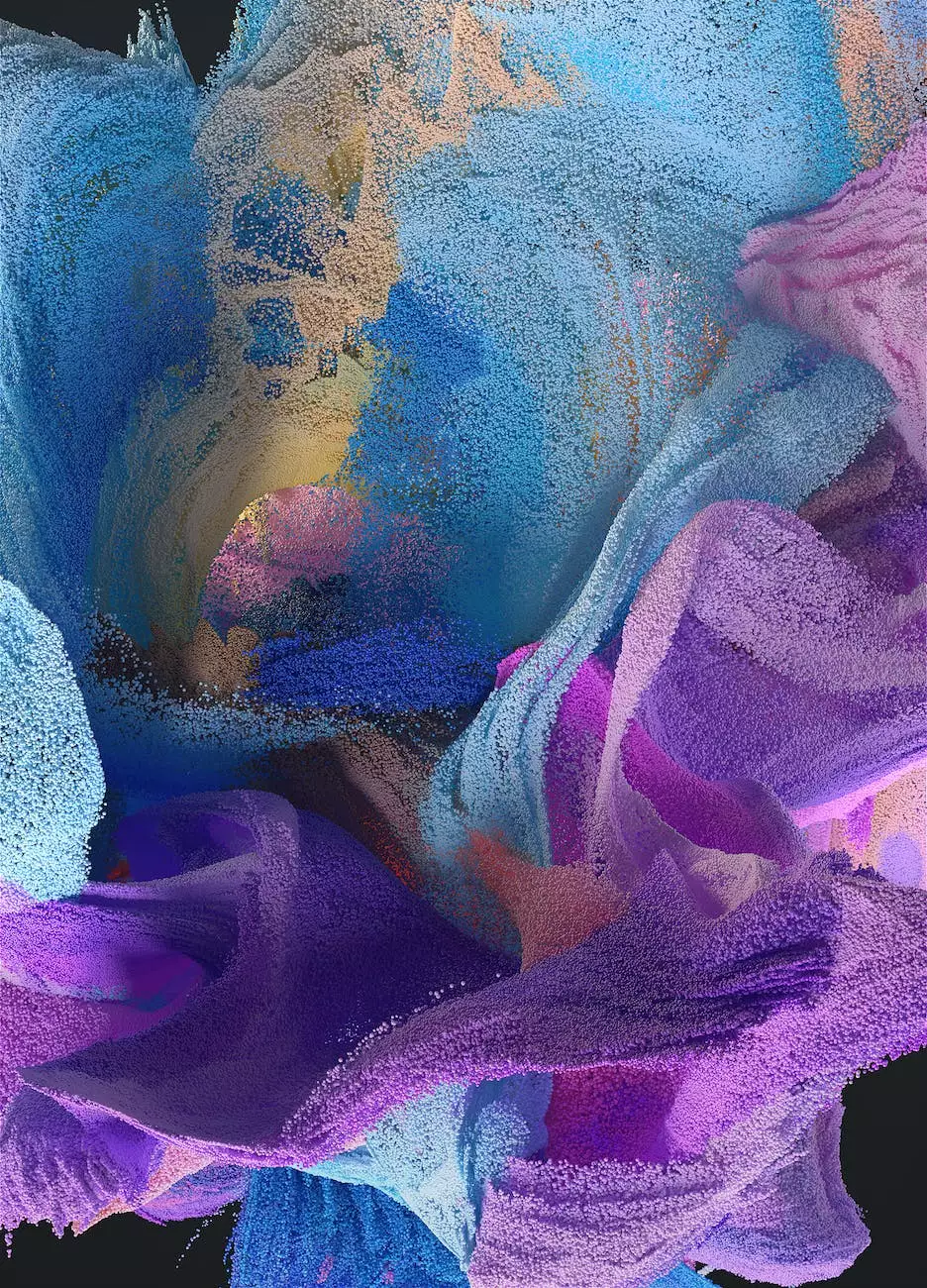
Welcome to Plastic Molding Pros, your trusted source for cutting-edge solutions in the eCommerce & Shopping - Manufacture category. In this article, we will discuss how 3D printing technology is revolutionizing the sand casting process, bringing numerous benefits to manufacturers in terms of cost, time, and quality.
The Advantages of 3D Printing in Sand Casting
3D printing has emerged as a game-changer in the world of manufacturing, particularly in sand casting. The traditional sand casting process involves creating molds and cores using sand, which can be time-consuming and labor-intensive. With the introduction of 3D printing, manufacturers can now streamline and optimize this process, resulting in significant advantages:
- Faster Production: 3D printing enables the creation of intricate molds and cores with complex geometries in a fraction of the time compared to traditional methods. This leads to faster production cycles and reduced time-to-market for plastic molding products.
- Cost Savings: By eliminating the need for expensive tooling and reducing material waste, 3D printing offers cost-effective manufacturing solutions. Manufacturers can also achieve economies of scale by easily adjusting designs and manufacturing multiple iterations without incurring additional expenses.
- Design Freedom: With 3D printing, designers have the freedom to create highly intricate and customized molds and cores that were previously not feasible. This unlocks new possibilities for product innovation and differentiation in the competitive marketplace.
- Improved Quality: 3D printed molds and cores offer enhanced dimensional accuracy, reducing the risk of defects and improving overall product quality. The ability to create complex internal structures and features also facilitates improved part performance and functionality.
The Evolution of Sand Casting through 3D Printing
The integration of 3D printing technology with sand casting has resulted in several advancements that are transforming the manufacturing landscape:
1. Enhanced Mold and Core Design
Traditional sand casting often imposes limitations on design complexity due to the constraints of sand molding. 3D printing allows for the creation of intricate designs with internal channels, complex cavities, and other features that were previously impossible to achieve. This opens up new opportunities for innovation and optimization in the production of plastic molding products.
2. Increased Efficiency in Pattern Making
Pattern making, a critical step in sand casting, involves creating patterns that serve as templates for molding sand. 3D printing enables the production of highly precise patterns with minimal manual labor. This reduces the time and effort required for pattern making, enabling manufacturers to expedite the overall production process.
3. Elimination of Tooling Costs
Traditional sand casting often requires the production of costly tooling, such as patterns and core boxes. With 3D printing, manufacturers can bypass this step, as the molds and cores can be directly printed from digital designs. This eliminates the need for expensive tooling, making sand casting a more cost-effective manufacturing method.
4. Rapid Prototyping and Iteration
3D printing allows for quick prototyping and iteration of designs, enabling manufacturers to rapidly validate and refine their concepts. This iterative approach not only promotes faster development cycles but also reduces the risk of costly errors and design flaws. Manufacturers can optimize their plastic molding products by easily making modifications and improvements as needed.
5. Improved Product Quality and Consistency
3D printed molds and cores offer exceptional dimensional accuracy and consistency, resulting in superior product quality. The ability to precisely control the deposition of sand material ensures consistent reproduction of intricate features, reducing the variability seen in traditional sand casting methods. This enhances the overall performance and reliability of the manufactured plastic molding products.
Neometrixtech.com: Your Expert Partner in 3D Printing for Sand Casting
At Neometrixtech.com, we specialize in leveraging the power of 3D printing to revolutionize sand casting processes. With our state-of-the-art technology, extensive expertise, and commitment to excellence, we provide our clients with top-notch solutions for manufacturing high-quality plastic molding products.
As leaders in the field, we understand the importance of staying ahead of the curve. Our team of skilled professionals is dedicated to continuously exploring innovative approaches that maximize the benefits of 3D printing in sand casting.
When you choose Neometrixtech.com as your partner, you can expect:
- Customized Solutions: We work closely with our clients to understand their specific requirements and deliver tailored solutions that meet their unique needs. Our personalized approach ensures the successful realization of your vision.
- Cutting-Edge Technology: Our advanced 3D printers and software tools enable us to produce highly intricate molds and cores with exceptional precision and accuracy. We are always at the forefront of technological advancements, ensuring optimal results for your projects.
- Reliability and Trust: With years of experience in the industry, we have earned a reputation for delivering reliable and high-quality solutions. Our commitment to excellence and our dedication to customer satisfaction set us apart as a trusted partner.
- Cost-Effective Services: We understand the importance of cost efficiency without compromising on quality. Our services are competitively priced to provide our clients with excellent value for their investment.
- Timely Delivery: We prioritize prompt delivery to meet your project timelines. Our efficient processes and agile production capabilities ensure that your plastic molding products are delivered on time, every time.
Get in touch with us today to discover how 3D printing can revolutionize your sand casting processes and take your plastic molding products to the next level.