A Guide To Wall Shear Stress Measurement - #3 - Direct Measurements
Blog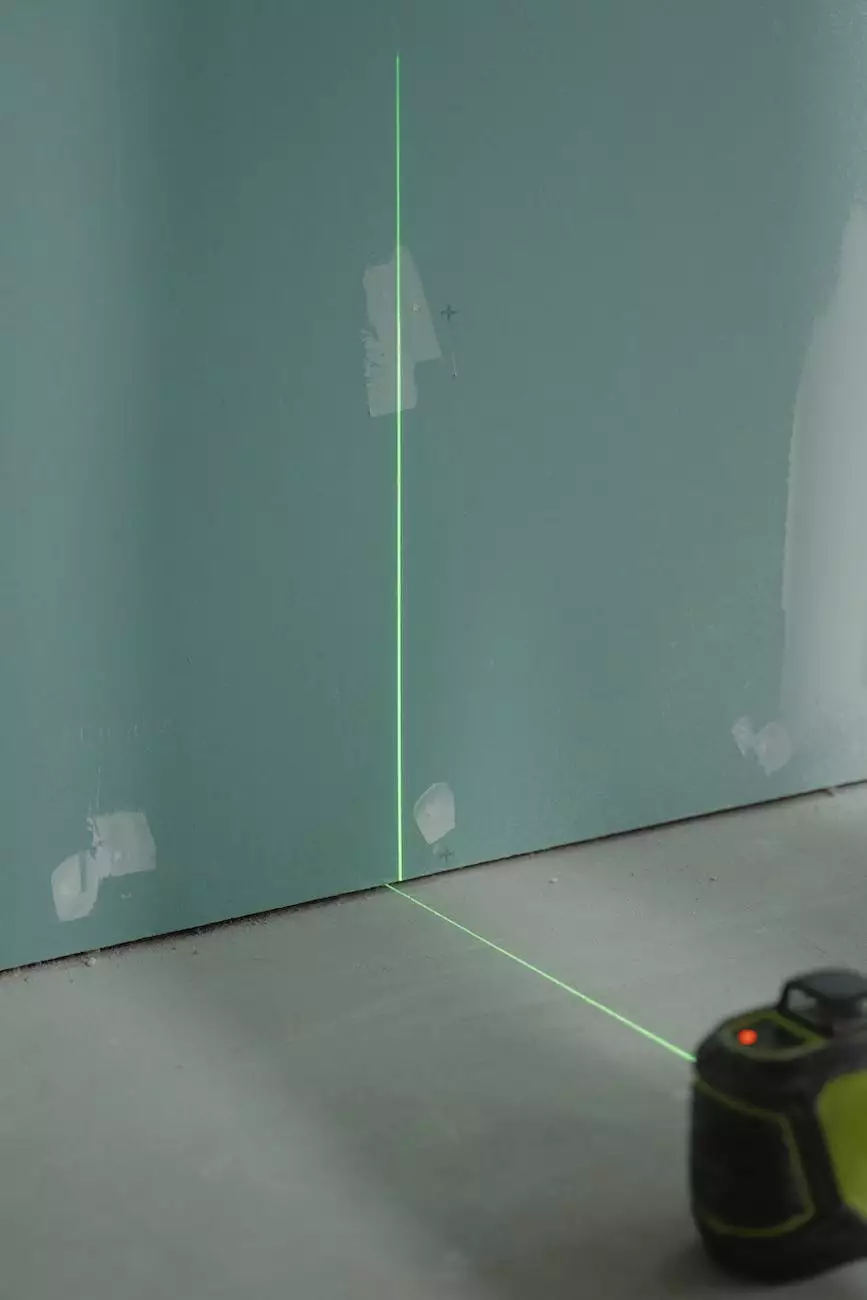
Introduction
Welcome to Plastic Molding Pros, your go-to resource for all things related to wall shear stress measurement in the field of plastic molding. In this comprehensive guide, we will delve into the third part of our series on measuring wall shear stress, focusing specifically on direct measurements.
Understanding Wall Shear Stress
Before we dive into the details of direct measurements, let's briefly recap what wall shear stress is and why it is crucial in the plastic molding industry. Wall shear stress refers to the force per unit area acting parallel to a surface, particularly the surface of a flow channel, like a mold cavity.
In plastic molding, wall shear stress plays a vital role in determining the flow behavior of the plastic material within the mold. It directly influences factors such as material distribution, mold filling, cooling, and part quality. Accurate measurement and control of wall shear stress are essential for optimizing production and ensuring consistent, high-quality plastic parts.
Benefits and Limitations of Direct Measurements
Direct measurements offer a more precise and accurate way of determining wall shear stress compared to indirect methods. By directly measuring the forces acting on a surface, such as using specialized sensors or pressure transducers, we can obtain real-time data that reflects the actual shear stress experienced by the material.
Direct measurements provide valuable insights into the dynamic changes of wall shear stress during the molding process, allowing for improved process control and troubleshooting. However, it is essential to consider the limitations of direct measurements, such as sensor selection, installation techniques, and potential interference with the flow behavior.
Types of Direct Measurement Techniques
1. Surface Shear Stress Sensors
Surface shear stress sensors are designed to directly measure the shear stress acting on the surface of the mold. These sensors can be mounted at strategic locations within the mold cavity, providing real-time data on the shear stress distribution during the molding process. Various technologies, such as piezoelectric, capacitive, or optical sensors, are used to capture the shear stress values accurately.
2. Pressure Transducers
Pressure transducers are widely used in the plastic molding industry to directly measure wall shear stress. These transducers are mounted in the mold cavity or in the runner system and provide continuous pressure readings, which can be correlated to shear stress levels.
3. Drag Flow Sensors
Drag flow sensors are specifically designed to measure wall shear stress by analyzing the drag forces exerted on a small probe inserted in the flow channel. These sensors are ideal for capturing the shear stress distribution during the molding process and are often used in research and development settings.
Considerations for Accurate Direct Measurements
When employing direct measurement techniques for wall shear stress, it is crucial to ensure accuracy and reliability. Here are some key considerations:
- Calibration: Regular calibration of the sensors or transducers is essential to maintain accuracy and validity of the measurements.
- Placement: Proper placement of the sensors within the mold cavity or runner system is critical for obtaining representative data.
- Temperature Compensation: Wall shear stress is affected by temperature variations within the mold. Implementing temperature compensation techniques improves measurement accuracy.
- Data Analysis: Collecting and analyzing data from direct measurements allows for valuable insights into process optimization and troubleshooting.
Conclusion
In conclusion, direct measurements provide an accurate and insightful approach to wall shear stress measurement in plastic molding. Plastic Molding Pros is dedicated to providing valuable resources and guides like this one to support professionals in the eCommerce & Shopping - Manufacture category. By understanding the significance of wall shear stress and utilizing direct measurement techniques, manufacturers can enhance production, improve part quality, and achieve optimal outcomes. Stay tuned for more informative content from Plastic Molding Pros!