Comprehensive Insights into Automobile Plastic Mold Manufacturing: The Expertise of Leading Metal Fabricators
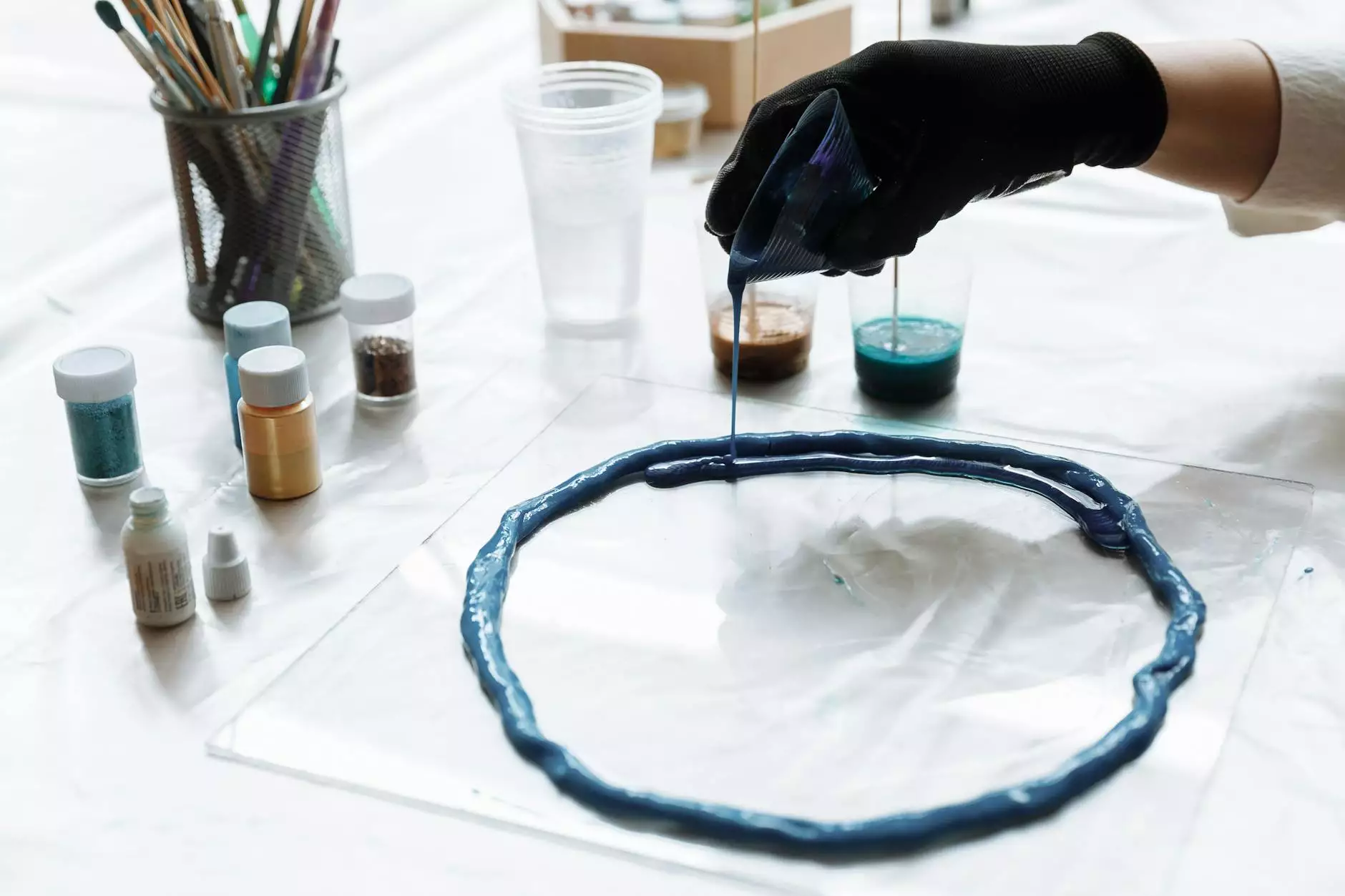
In the rapidly evolving world of automotive manufacturing, precision, durability, and innovation are paramount. One of the critical components ensuring these qualities is the automobile plastic mold. As the backbone of many high-quality automotive parts, the manufacturing of these molds demands an exceptional level of expertise, advanced technology, and rigorous quality control. Leading metal fabricators like deepmould.net have perfected the art of crafting superior automobile plastic molds.
Understanding the Role of Automobile Plastic Molds in Automotive Manufacturing
Automobile plastic molds serve as the foundational tooling for creating complex plastic components used throughout vehicles—from interior panels and bumpers to lighting fixtures and engine covers. The quality of these molds profoundly influences the final product's appearance, functional integrity, and longevity.
Modern automotive plastic molds are designed to meet the rigorous demands of high-volume production while maintaining tight tolerances. This requires an intricate blend of craftsmanship, cutting-edge technology, and material science expertise housed within top-tier metal fabricators.
The Significance of Advanced Technologies in Automobile Plastic Mold Production
In recent years, technological advancements have revolutionized the way molds are manufactured. Leading metal fabricators leverage a suite of modern tools including:
- CNC Machining: Offers unparalleled precision in shaping molds to exact specifications and complex geometries.
- Electric Discharge Machining (EDM): Enables detailed features and intricate designs that are otherwise impossible with conventional machining.
- 3D Printing & Additive Manufacturing: Facilitates rapid prototyping and complex insert creation, reducing lead times.
- Surface Finishing Technologies: Processes like abrasive blasting and plating ensure optimized surface quality for seamless molding and aesthetic appeal.
These technologies empower metal fabricators like deepmould.net to produce high-precision, durable, and functionally superior automobile plastic molds.
Material Selection and Design Optimization for the Perfect Automobile Plastic Mold
Careful consideration of mold materials is crucial for achieving optimal performance. The choice typically involves high-grade tool steels such as P20, H13, or S7, which offer excellent toughness, high-temperature resistance, and corrosion resistance. These materials ensure the mold's longevity under high-volume production cycles.
Design optimization also plays a vital role, balancing factors like cooling efficiency, material flow, and degassing. Advanced simulations and finite element analysis (FEA) tools are extensively used by top modern metal fabricators to refine mold design before physical manufacturing begins.
The Process of Manufacturing Automobile Plastic Molds: From Concept to Completion
The manufacturing workflow involves several meticulously coordinated stages, each handled by expert professionals in the field:
1. Concept & Design
Initial specifications and functions are translated into detailed CAD models. High-level design considerations include ease of manufacturing, parting line placement, and cooling channels.
2. Material Selection & Prototype Development
Choosing the right materials and creating prototypes for validation ensures the design meets all functional and aesthetic requirements.
3. Precision Machining & Fabrication
Using CNC and EDM processes, the core and cavity are machined with high accuracy, ensuring the parts conform strictly to design specifications.
4. Surface Finishing & Assembly
Surface treatments like polishing and texturing optimize mold release and aesthetic finishes. During assembly, all components are meticulously checked for fit and function.
5. Testing & Validation
Molds undergo trial runs with actual plastics, allowing for adjustments to ensure defect-free, high-quality production runs.
Key Qualities That Make Leading Metal Fabricators Stand Out in Producing Automobile Plastic Molds
Excellence in creating automobile plastic molds hinges on several core qualities demonstrated by top-tier metal fabricators:
- Technical Expertise: Deep understanding of material science, mold design, and manufacturing processes.
- Innovative Capabilities: Adoption of the latest technology for increased efficiency and precision.
- Quality Assurance: Rigorous testing, inspection, and adherence to international standards.
- Customer Focus: Custom solutions tailored to specific project requirements and collaboration throughout the development cycle.
- Environmental Responsibility: Implementation of eco-friendly practices, sustainable materials, and waste reduction techniques.
Why Choose Deepmould.net for Your Automobile Plastic Mold Needs?
As a leading metal fabricator specializing in high-precision tooling and automobile plastic molds, deepmould.net exemplifies excellence in manufacturing. Their commitment to innovation, quality, and customer satisfaction ensures that every mold they produce meets the highest standards.
With extensive experience working with automotive OEMs and Tier 1 suppliers, deepmould.net provides:
- Custom designed molds tailored to specific automotive components.
- Quick turnaround times without compromising on quality.
- Comprehensive post-processing and maintenance services.
- Innovative solutions utilizing the latest in CAD/CAM, CNC, and EDM technology.
The Future of Automobile Plastic Molds in the Automotive Industry
The automotive industry is witnessing a paradigm shift driven by electric vehicles (EVs), autonomous driving, and smart manufacturing. Consequently, the demand for highly specialized automobile plastic molds continues to grow, requiring innovations like:
- Enhanced material technologies for high-temperature and chemical resistance.
- Smart mold technologies incorporating sensors for real-time monitoring.
- Sustainable manufacturing practices focused on reducing environmental impact.
- Modular mold designs for flexibility and faster adaptation to new vehicle models.
Leading metal fabricators are at the forefront of these technological innovations, ensuring that the production of automobile plastic molds remains efficient, cost-effective, and aligned with future automotive trends.
Choosing the Right Partner for Your Automobiles Plastic Mold Projects
Successful mold manufacturing requires a partner with proven expertise, technological prowess, and a commitment to quality. When selecting a metal fabricator:
- Verify their experience in automotive mold manufacturing.
- Review their technological capabilities and certifications.
- Assess their portfolio of successful projects and client testimonials.
- Ensure they adhere to international quality standards such as ISO 9001 and IATF 16949.
- Evaluate their after-sales support and ongoing maintenance services.
Partnering with a reputable provider like deepmould.net guarantees access to the latest in mold manufacturing innovation and a dedicated team committed to excellence.
Conclusion
In the high-stakes world of automotive manufacturing, automobile plastic molds are pivotal to producing superior, reliable, and aesthetically appealing components. The expertise of leading metal fabricators such as deepmould.net ensures that the molds not only meet but exceed industry standards, enabling automotive manufacturers to innovate confidently. By prioritizing precision engineering, advanced technology adoption, and quality assurance, these companies continue to push the boundaries of what is possible in automotive mold manufacturing, securing a robust future for automotive innovation worldwide.