Understanding the Role of China Die Casting Manufacturers in Metal Fabrication
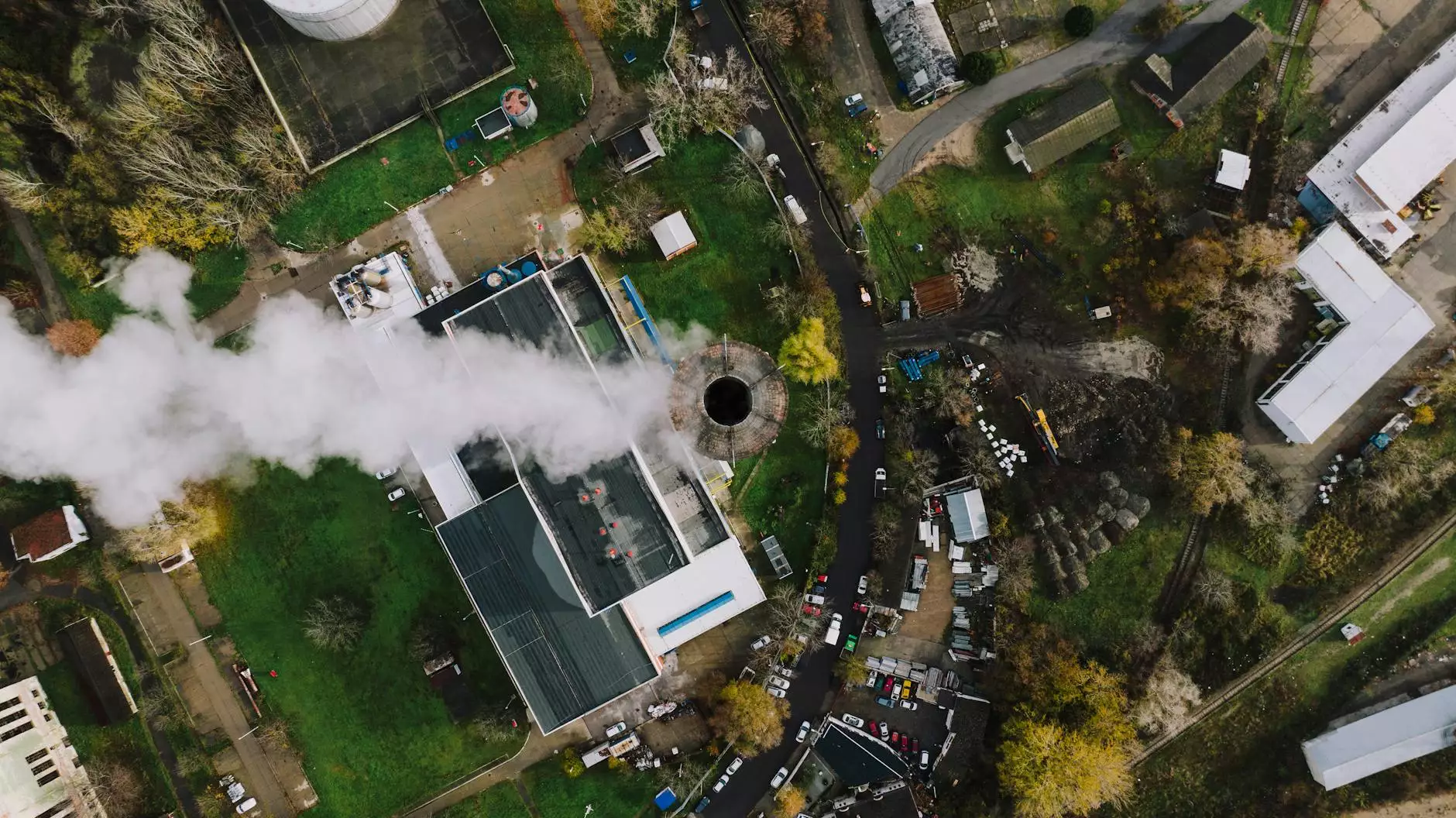
As industries evolve, the need for high-quality components becomes more pronounced, leading to a booming demand for specialized manufacturing processes. Among these processes, die casting stands out, primarily due to its capability to produce intricate shapes and forms with exceptional accuracy. Within the realm of die casting, China die casting manufacturers have established themselves as formidable players in the global market.
What is Die Casting?
Die casting is a manufacturing process where molten metal is injected into a mold under high pressure. This technique allows for the production of complex shapes and tight tolerances, significantly reducing the need for machining and other secondary processes. The die casting process typically involves non-ferrous metals such as aluminum, zinc, and magnesium, which are preferred for their lightweight and durable qualities.
The Evolution of Die Casting in China
The history of die casting in China dates back several decades. Initially, the industry was characterized by low-capacity and low-precision operations. However, with advancements in technology and significant investments, China die casting manufacturers have evolved into high-tech enterprises capable of producing components for various applications, including automotive, aerospace, and consumer electronics.
- Historical Growth: The transformation of the die casting industry in China reflects the overall industrialization of the country, marked by rapid development and technological advancement.
- Technological Advancements: Modern Chinese manufacturers utilize state-of-the-art machinery and techniques, resulting in high-quality finished products.
Why Choose China Die Casting Manufacturers?
Companies around the world often look to China die casting manufacturers for several compelling reasons:
- Cost Efficiency: With lower labor costs and high production capacities, manufacturers in China can offer competitive pricing without compromising quality.
- Quality Control: Many Chinese factories adhere to strict quality management systems, ensuring that products meet international standards.
- Versatility: Capable of producing a wide variety of parts for different industries, including automotive, medical, and electronics.
- Scalability: Large manufacturers can scale production to meet the demands of businesses, from small to large volume orders.
Key Advantages of China Die Casting Manufacturers
1. Technological Leadership
Chinese manufacturers have invested in advanced die casting technology, including:
- Computer Numerical Control (CNC) Machines: Enhancing precision and enabling complex geometries.
- Robotic Automation: Streamlining production processes and reducing human error.
2. Comprehensive Service Offerings
Beyond die casting, many manufacturers provide integrated services, including:
- Design Assistance: Working with clients to optimize product design for manufacturability.
- Post-Processing Services: Additional machining, finishing, and assembly services.
3. Strong Supply Chains
China's manufacturing ecosystem benefits from robust supply chains, facilitating the procurement of raw materials and components, which enhances turnaround times and reliability.
The Die Casting Process: How It Works
- Mold Preparation: Designing and preparing the die mold to the desired specifications.
- Melting Metal: Heating the metal to its liquid state to prepare for casting.
- Injection: Injecting the molten metal into the mold under high pressure.
- Cooling: Allowing the metal to cool and solidify within the mold.
- Die Extraction: Removing the newly formed part from the mold.
- Finishing: Performing any necessary post-processing to achieve the final product specifications.
Quality Standards in Die Casting
Quality is paramount in die casting, especially in industries where safety and performance are critical. China die casting manufacturers adhere to various international quality standards, ensuring that their products meet the stringent requirements of global markets.
These standards may include:
- ISO 9001: Focusing on quality management systems.
- IATF 16949: Specific to the automotive sector, ensuring high-quality production processes.
- RoHS Compliance: Ensuring that products are free from hazardous substances.
Challenges Faced by China Die Casting Manufacturers
Despite the many advantages, China die casting manufacturers face several challenges:
- Competition: As the global demand increases, so does competition from manufacturers in other regions.
- Environmental Regulations: Stricter environmental standards are being imposed, requiring manufacturers to adopt green practices.
- Technological Adaptation: Continuously upgrading technology to stay relevant can be a significant investment.
The Future of Die Casting in China
The future of die casting in China appears promising as manufacturers adapt to global trends and demands. Innovations in technology, coupled with a focus on sustainability, are likely to shape the industry moving forward.
Key trends that may influence the future include:
- Smart Manufacturing: The integration of IoT and AI to enhance production efficiency.
- Sustainability Initiatives: A shift towards more eco-friendly practices in manufacturing.
- Market Expansion: Addressing emerging markets and expanding the portfolio of products offered.
Conclusion
In summary, China die casting manufacturers play a crucial role in the global manufacturing ecosystem, particularly in the metal fabrication sector. With a robust combination of technology, quality control, and experience, they have established themselves as leaders in the industry. As the demand for high-quality, cost-effective, and agile manufacturing grows, so too will the importance of these manufacturers in meeting the needs of various sectors.
To learn more about partnering with top-tier China die casting manufacturers, consider exploring the offerings at DeepMould, where innovation meets quality in metal fabrication.