Pumps in Hydraulics: The Heart of Modern Machinery
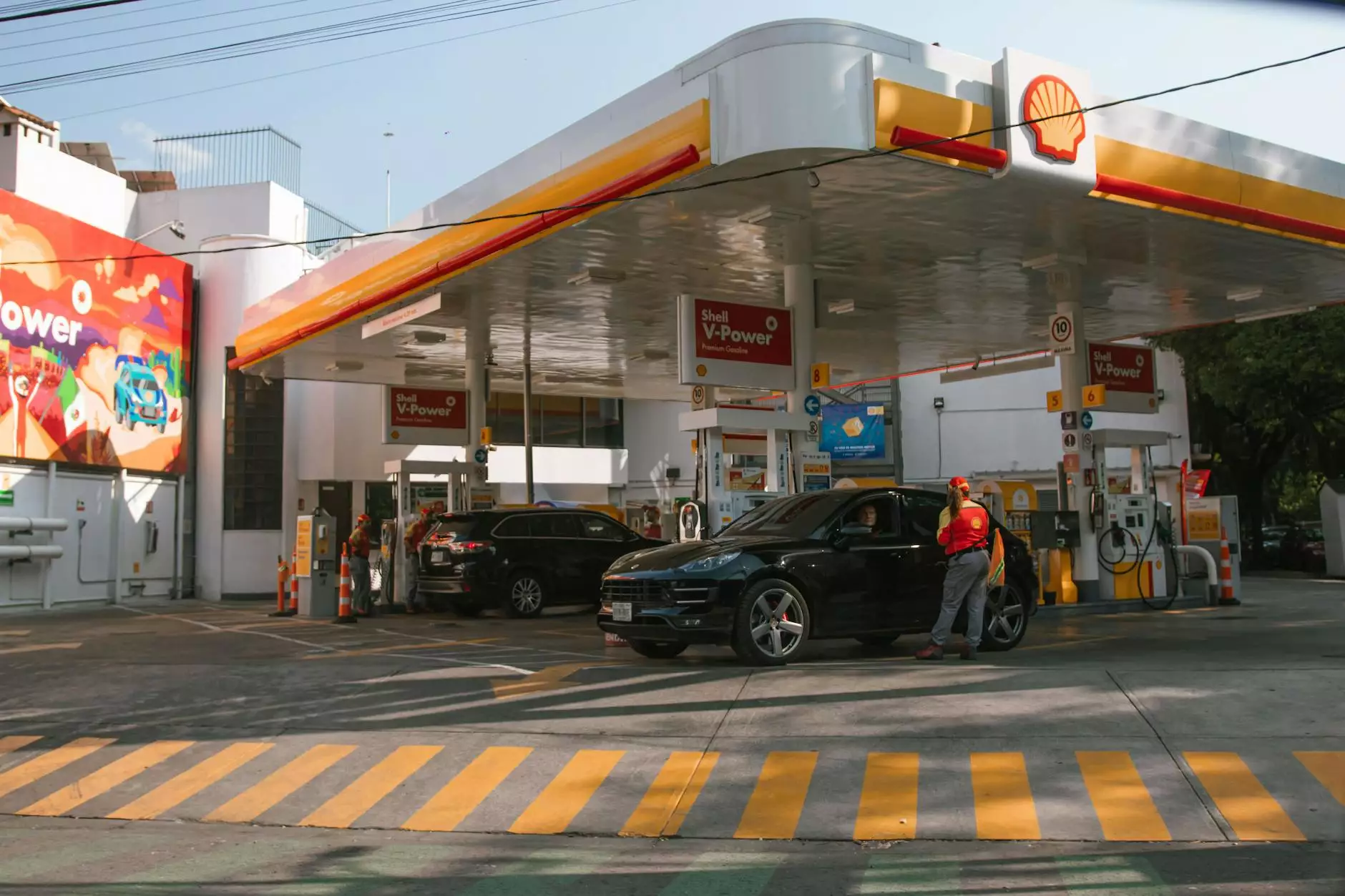
In the world of machinery and automotive technology, pumps in hydraulics play a fundamental role in ensuring smooth operation and unparalleled efficiency. This article dives deep into understanding hydraulic pumps, their classifications, functions, and importance within various applications. Hydraulics is a domain that significantly impacts both auto and motorcycle parts, influencing efficiency from the ground up.
Understanding Hydraulic Systems
Hydraulic systems utilize liquid fluid power to perform work. The liquid, usually hydraulic oil, transmits energy from one location to another. Hydraulic systems have numerous applications, including construction machinery, automotive products, and more. This efficiency is primarily due to the use of hydraulic pumps, which are the heart of the system.
The Role of Pumps in Hydraulics
Pumps in hydraulics are crucial components that convert mechanical energy into hydraulic energy. They draw fluid from a reservoir and pressurize it, allowing it to flow through the system and do useful work. Here’s a more detailed look at their functions:
- Fluid Movement: Pumps enable the movement of hydraulic fluid throughout the system.
- Pressure Generation: They create and maintain the necessary pressure to operate hydraulic machinery.
- Efficiency Boost: By minimizing fluid losses and enabling precise control, pumps enhance overall system efficiency.
Types of Hydraulic Pumps
There are several types of hydraulic pumps, each designed to accommodate different applications and specifications. The two primary types are dynamic pumps and positive displacement pumps.
1. Dynamic Pumps
Dynamic pumps rely on the kinetic energy of a rotating element to move hydraulic fluids. They are typically used in applications requiring high flow rates but lower pressures. Key characteristics include:
- High Flow Rates: Ideal for applications needing substantial fluid movement.
- Lower Operational Costs: Often less expensive and easier to maintain.
2. Positive Displacement Pumps
Positive displacement pumps move a specific amount of fluid with each stroke or rotation, creating high pressure in the process. They are vital for applications requiring precise flow control. Features include:
- Consistent Flow: Provide a steady flow rate regardless of outlet pressure.
- High Efficiency: Extremely efficient for generating high pressures, making them suitable for heavy-duty applications.
Importance of Hydraulic Pumps in Auto Parts & Supplies
Hydraulic pumps are indispensable in auto parts, particularly in systems that require precise control and reliability. Common applications include:
- Brake Systems: Hydraulic pumps are used in braking systems, where they apply pressure to brake fluid, allowing for effective stopping performance.
- Power Steering: Many modern vehicles utilize hydraulic pumps to assist in steering, enhancing driver comfort and vehicle maneuverability.
- Suspension Systems: Hydraulic components in active suspension systems adjust the car's stiffness, improving ride quality and handling.
Hydraulic Pumps in Motorcycle Parts & Supplies
In motorcycles, the agility and precision of hydraulic systems contribute significantly to performance. Here’s how hydraulic pumps enhance motorcycle functioning:
- Braking Performance: Just like in cars, hydraulic brakes are crucial for effective stopping power and rider safety.
- Clutch Control: Many motorcycles use hydraulic clutches, which provide smoother engagement and disengagement compared to cable-operated systems.
- Suspension & Damping: Hydraulic systems in motorcycle suspensions allow for adjustments that enhance both comfort and handling capabilities.
Advantages of Hydraulic Pumps
The adoption of hydraulic pumps in various mechanical systems offers several notable benefits:
- High Power Density: Hydraulic systems can transmit large amounts of energy through relatively small components.
- Flexibility: They can be used in a wide range of applications, from industrial machinery to personal vehicles.
- Compact Design: Many hydraulic pumps are designed to fit in tight spaces, allowing for integration into smaller systems.
- Durability: With proper maintenance, hydraulic pumps can operate for many years without significant wear.
Maintenance Tips for Hydraulic Pumps
To keep pumps operating at peak efficiency, regular maintenance is essential. Here are some practical tips:
- Fluid Checks: Regularly inspect hydraulic fluid levels and quality to prevent damage and inefficiency.
- Filter Cleaning/Replacement: Maintain clean filters to avoid contamination that can damage system components.
- Inspect Hoses and Fittings: Regularly check hoses and connections for signs of wear or leaks, which can severely impact performance.
- Monitor Pressure Levels: Keeping an eye on pressure readings ensures that the system operates within its optimal range.
Conclusion
In summary, pumps in hydraulics are essential to modern machinery, including both auto and motorcycle parts. Their ability to convert mechanical energy into hydraulic energy has revolutionized various industries, making tasks easier, safer, and more efficient. With an understanding of the types, benefits, and maintenance of hydraulic pumps, operators can maximize their performance, ensuring reliability and safety in every application.
For superior performance parts and supplies, including hydraulic components, visit Shop Hydraulic America. Your destination for quality and reliability in hydraulic systems.