The Ultimate Guide to Hydraulic Final Drive Systems
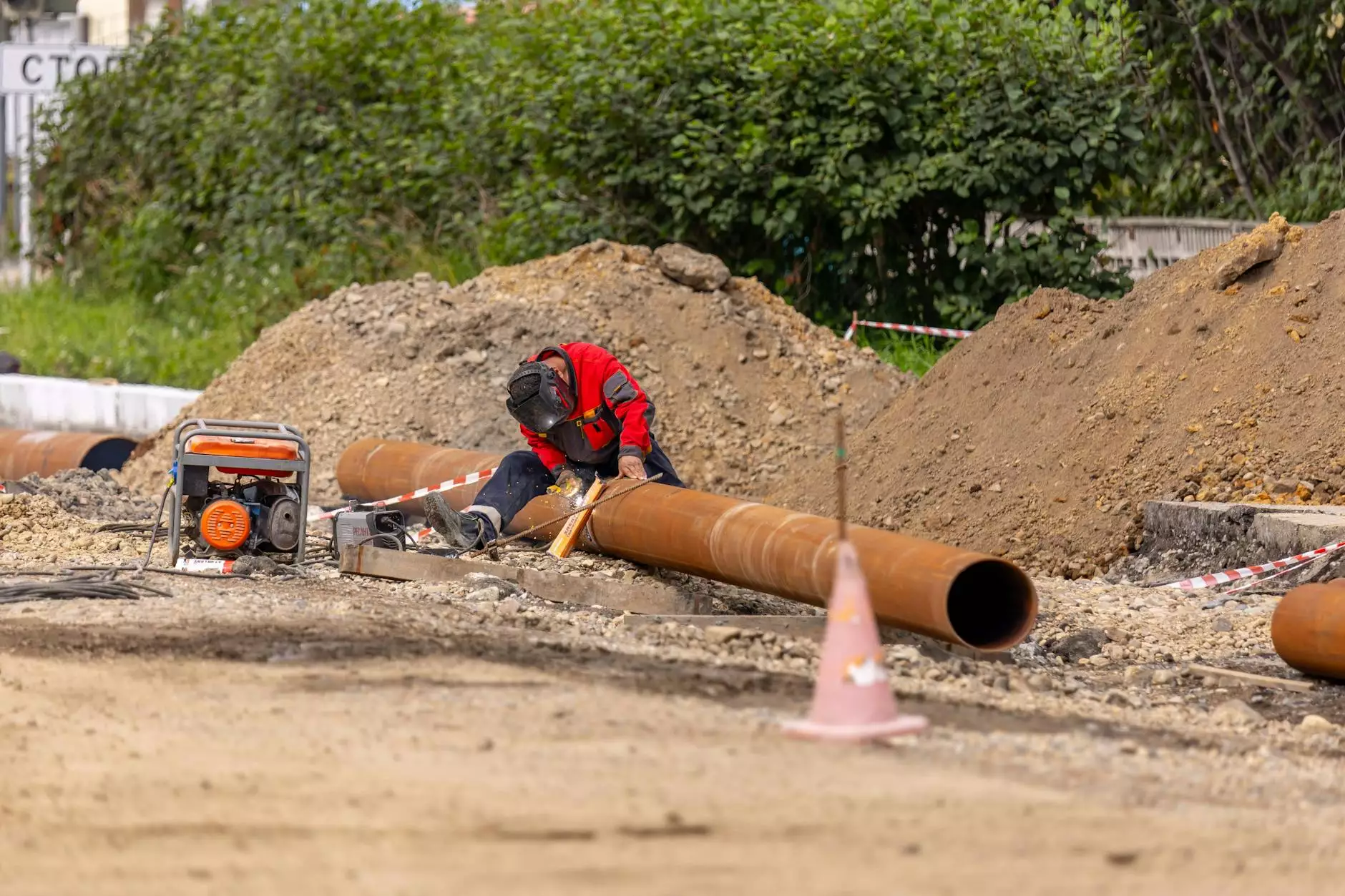
In today's world of machinery and heavy equipment, the term hydraulic final drive emerges as a crucial component that significantly enhances operational efficiency. This comprehensive article delves into the intricate details of hydraulic final drive systems, their functionality, advantages, applications, and maintenance practices. Perfect for construction, agricultural, and industrial sectors, understanding this component can lead to substantial benefits for business operations.
What is a Hydraulic Final Drive?
A hydraulic final drive is a mechanical assembly that connects the hydraulic system of machinery to the drive wheel or track, enabling the equipment to move. It functions as a speed-reducing unit that converts the high rotational speed of the hydraulic motor into low-speed torque, which is essential for driving heavy loads.
Components of a Hydraulic Final Drive
The hydraulic final drive consists of several key components:
- Hydraulic Motor: This is the powerhouse of the system, converting hydraulic energy into mechanical energy.
- Planetary Gear System: This system reduces the speed while increasing torque output, allowing for better handling of heavy machinery.
- Final Drive Housing: This structure houses the components and protects them from external elements.
- Output Shaft: This connects the final drive to the wheel or track, transferring the power generated by the motor.
How Does a Hydraulic Final Drive Work?
The functionality of a hydraulic final drive can be summarized in the following steps:
- The hydraulic pump generates fluid pressure, which is directed to the hydraulic motor.
- The hydraulic motor converts this fluid pressure into mechanical power.
- This power is transmitted through a planetary gear set that reduces speed and increases torque.
- Finally, the output shaft delivers the rotational force to the machinery's wheel or track.
Benefits of Hydraulic Final Drive Systems
Hydraulic final drives offer numerous advantages that make them preferable in many industrial applications:
- Compact Design: Hydraulic final drives are generally smaller and lighter than traditional drive systems, making them ideal for compact machinery.
- High Torque Output: They provide exceptional torque, essential for moving heavy loads with ease.
- Smooth Operation: The hydraulic system ensures a smoother operation with fewer vibrations.
- Energy Efficiency: These systems are designed to deliver optimal performance while minimizing energy consumption.
- Durability: Well-designed hydraulic final drives are robust and can operate in challenging environments.
Applications of Hydraulic Final Drive
Hydraulic final drives are widely used across various industries, including:
1. Construction Equipment
In excavators, compact track loaders, and other heavy machinery, hydraulic final drives provide the required power and maneuverability to perform demanding tasks.
2. Agricultural Machinery
Tractors and harvesters utilize hydraulic final drives to ensure efficient operation across varying terrains and heavy loads.
3. Mining Equipment
In the mining industry, hydraulic final drives are essential for operating equipment that requires high torque to handle heavy loads in difficult conditions.
4. Material Handling Equipment
Forklifts and telehandlers rely on hydraulic final drives for effective lifting and transport of goods.
Choosing the Right Hydraulic Final Drive
Selecting the appropriate hydraulic final drive for your application is critical for optimizing performance. Here are key considerations:
- Torque Requirements: Calculate the necessary torque for your specific application.
- Speed Ratios: Ensure the final drive can achieve the desired speed while handling load requirements.
- Compatibility: Verify that the hydraulic final drive is compatible with your machine's hydraulic system.
- Environment: Consider environmental factors such as temperature, moisture, and dust when selecting a drive.
Maintenance of Hydraulic Final Drives
Regular maintenance of hydraulic final drives is essential for longevity and performance. Below are some critical maintenance practices:
1. Regular Fluid Checks
Check hydraulic fluid regularly to ensure optimal performance. Low fluid levels can lead to overheating and component failure.
2. Inspect for Leaks
Periodic inspections for leaks can prevent major failures. Address any leaks promptly to avoid damage to the hydraulic system.
3. Gear Lubrication
Ensure that the gears are adequately lubricated to minimize wear and maintain smooth operation.
4. Monitor Performance
Keep track of the system's performance. Any sudden changes in operation could indicate a problem that needs addressing.
Conclusion
The hydraulic final drive plays a vital role in modern machinery, driving efficiency, performance, and reliability. By understanding its components, benefits, and maintenance requirements, businesses can optimize their operations and ensure their equipment runs smoothly and efficiently. Whether you’re in construction, agriculture, or other sectors, investing in a quality hydraulic final drive system from a reputable supplier like Shop Hydraulic America can lead to significant operational advantages.
Further Learning and Resources
If you want to delve deeper into the world of hydraulic systems and final drives, consider the following resources:
- Shop Hydraulic America Blog: Regularly updated insights on hydraulic systems.
- Technical Resources: Detailed manuals and specifications for various hydraulic components.
- Contact Us: For personalized support and product inquiries.
By leveraging reliable information and resources, businesses can enhance their knowledge and application of hydraulic final drives, leading to improved performance and success in their respective fields.